
Über den Autor:
CEO bei AlFiPa, verantwortlich für das operative Geschäft sowie Einkauf und Verkauf. Er ist der Hauptansprechpartner für Bestellungen und Lieferungen im Unternehmen.
Neben den Qualitäten von Produkten, zählen heute einmal mehr die Verpackungen, die Waren erst richtig präsentieren. Kaum vorstellbar, wie es wäre Parfüm nicht in einem hochwertigen Flakon präsentiert zu bekommen, aber auch das neue Smartphone wäre in einem schlichten Karton sicherlich nicht angemessen verpackt.
Oberflächen spielen hierbei eine wichtige Rolle. Neben den dekorativen und optischen Ansprüchen an Oberflächen, spielt aber auch die funktionale Veredelung von Oberflächen eine zunehmende Rolle. Die meisten Waren, insbesondere Lebensmittel, aber auch Medikamente oder Kosmetika stellen hohe Anforderungen an Verpackungen, für die wir maßgeschneiderte Lösungen für unsere Industriekunden anbieten.
Wir metallisieren, laminieren, beschichten und führen Prozesse durch, die Oberflächen optisch und funktional veredeln. Wir erstellen Sperrschichten, veredeln aber auch so nach Kundenwunsch, dass sich für Verbraucher der Umgang mit Verpackungen erleichtert.
Oberflächenvorbehandlung
In der Regel können Veredelungsverfahren nicht direkt auf oder in die vorhandene Verpackungsoberfläche eingebracht werden, sondern es bedarf einer Oberflächenvorbehandlung. Die vorbereitende Oberflächenbehandlung erfolgt insbesondere in der Gruppe der unpolaren Kunststoffe, wie PET, PE und PP. Der Prozess der Oberflächenvorbereitung ist die Voraussetzung für nachfolgende Veredelung, wie Bedrucken, aber auch Kaschieren oder beispielsweise Beschichtung. So vorbehandelte Oberflächen verfügen über eine bessere Benetzbarkeit, chemische Affinität und Adhäsion.
Zu den wichtigsten vorbereitenden Verfahren bei Folien zählen die antistatische Verarbeitung, die Coronaveredelung und Flammbehandlung. Sind diese Oberflächen vorbehandelt worden, können nachfolgende dekorative oder optische Veredelungsprozesse angeschlossen werden.
Antistatische Vorbehandlung:
Eine elektrostatische Aufladung ist erforderlich, da unbehandelte Materialoberflächen Staubpartikel anziehen, aber auch elektrische Schläge verursachen können. Oberflächen können wie folgt behandelt werden:
- Lackauftrag von Antistatika
- Oberflächenauftrag mit hochkonzentrierten Seifenlösungen (hydrostatisch)
- So genanntes Ausschwitzen von hygroskopischen oder antistatischen Additiven an der Oberfläche
- Ionisierende Behandlung über das Anbringen polarer Gruppen
- Bei den aufgeführten Behandlungen wird der Antistatik-Effekt über einen Wasserfilm erzeugt, der Ladung ableiten kann
Beflammen von Oberflächen:
Beim Beflammen wird eine oxidative Oberflächenbehandlung erzeugt. Die über eine Flamme bearbeitete Oberfläche verändert thermisch so die Eigenschaften, dass es zu einer besseren Haftung von Druckfarben oder anderen beispielsweise Etiketten kommt. Beim Verfahren werden polare Gruppen über Oxidation erzeugt.
PE und PP benötigen in besonderem Maße eine Beflammung. Aufgrund das Oberflächen chemisch inert und unpolar sind, bedürfen Polyethylen und Polypropylen dieser Behandlung, um eine bessere Haftung von Lacken und Druckfarben, aber auch Klebstoffen zu erhalten. Eines der Vorteile dieser Oberflächenbehandlung, liegen in den geringen Kosten und der verfahrenstechnisch einfachen Umsetzung.
Hochfrequenzentladung – Coronabehandlung:
In dem Oberflächenverfahren Coronabehandlung werden Kunststoffoberflächen einer Hochfrequenzentladung exponiert. Dabei wird unter Atmosphärendruck Oxidation in Gang gesetzt, die polare Gruppen erzeugt. Zwei Elektroden ionisieren dabei Luft und es kommt zu einem Zusammenwirken zwischen Elektronen, Ionen und UV-Strahlung auf die Oberfläche. Es entsteht ein Plasmastrom, in dessen Zusammensetzung von den Teilchen, energiereich aufgeladene Elektronen Wasserstoff abspalten.
Durch den oxidativen Abbau und Radikale, entstehen polare Gruppen, die die Oberflächenenergie erhöhen. Atomarer Sauerstoff und Ozon bilden im Entladungsraum polare Gruppen, die Polymerabbau erzeugen. Oft wird die Coronabehandlung fälschlicherweise als Ozonbehandlung bezeichnet.
Die Komponenten dieses Verfahrens sind ein Hochfrequenzgenerator und die Elektrodeneinheit. Über einen Generator wird eine hochfrequente Wechselstromspannung erzeugt. Eine Entladung erfolgt über Elektroden. Gebräuchliche Spannung bei diesem Verfahren liegen im Bereich zwischen 12-20KV und 20 kHz.
In der Oberflächenbehandlung zählen die Beflammung und Coronabehandlung zu den wichtigsten Verfahren bei Oberflächen. Kunststofffolien verfügen zwar über positive Merkmale, wie den elektrischen Isolierungseigenschaften, die in manchen Bereichen sehr wichtig sind, aber Kunststofffolien zum anderen schlecht benetzbar mit Klebern, Haftvermittlern oder Lösungsmittel machen. Ein Bedrucken solcher Folien oder das Weiterverarbeiten durch Kaschieren oder Beschichten ist folglich nicht möglich. Negative Folgen wären, dass Druckfarben nicht haften würden und auch bei Verbundfolien würde eine Delamination auftreten.
Die Coronabehandlung ist das am häufigsten angewendete Verfahren bei der Oberflächenbehandlung von Folien. Nachteil bei diesem Verfahren ist die Wirksamkeit der Coronabehandlung, die mit der Zeit abnimmt, sprich die so behandelten Folien verlieren durch Lagerung an ihren Eigenschaften.
Primer-Behandlung / Grundierung von Oberflächen:
Bei dieser Oberflächenbehandlung wird Grundierungsmittel aufgetragen, um so eine bessere Haftung zu erzeugen, die für eine nachfolgende Behandlung eine entscheidende Rolle übernimmt. Hier ist es insbesondere eine verbesserte Haftung bei bestimmten Feinblechen oder Folien beim Beschichten oder Bedrucken. Bei bestimmten Folien oder Packmitteln kommt es zu negativen Erscheinungen bei der Verwendung bestimmter Klebstoffe, so dass hier Haftprimer erforderlich sind. Beim Aufstreichen auf einen Trägerstoff lassen sich so weitere Verbesserungen in Hinblick auf Bedrucken, Dichtheit, Siegelbarkeit oder Oberflächenbeschaffenheit erzielen.
Dekorative & optische Veredelung
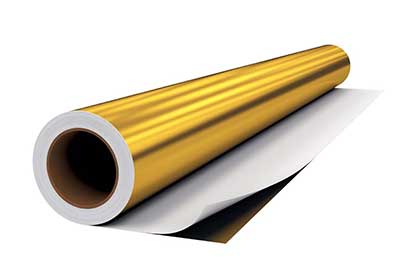
Dekorative Oberflächenveredelung von Kunststoffverpackungen
Neben den rein funktionalen Oberflächenbehandlungen, die technisch messbare Verbesserungen und Produkteigenschaften erzeugen, finden aber die dekorativen oder optischen Veredelungen immer mehr Eingang in die Bearbeitung von Oberflächen. Beispielsweise werden mit Prägefolien Druckbilder aufgebracht, lackiert, signiert, beklebt, lackiert oder beflockt, um ein Produkt zu veredeln. Als Hersteller und Lieferant der Industrie versorgen wir unsere Kunden mit Folien, Papieren und Verpackungsprodukten, die optische Eigenschaften hinsichtlich Transparenz, Glanz oder Trübung hervorrufen, aber auch bestimmte Werte beim Brechungsindex erreichen.
Druckverfahren:
Tiefdruck – die Rotogravur
Eines der wichtigsten Druckverfahren ist der Tiefdruck, der auch als Rotogravur bezeichnet wird. Insbesondere bei der Produktion von Folien und Verpackungen bietet die Rotogravur die vielseitigsten Einsatzmöglichkeiten, bei besten Druckeigenschaften auf der Oberfläche. In dem Druckverfahren werden die zu bedruckenden Stellen in der Druckform durch Gravur oder auch Ätzung vertieft, bei der man von so genannten Näpfen spricht, in die der Druck eingebracht wird. Bei der Einfärbung verbleibt die Farbe in den vorgesehenen Stellen. In den Bereichen, in denen kein Druck erfolgt, wird die Farbe über einen Rakel oder eine Wischvorrichtung entfernt. Mittels Tiefdruck auf Folien, sind so Drucke von Bildern in Fotoqualität realisierbar.
Offsetdruck
Offsetdruckverfahren wenden wir insbesondere bei Folienbahnen an. Es handelt sich um ein indirektes Flachdruckverfahren. Die zu bedruckenden Stellen liegen hierbei höher, als die Stellen, die unbedruckt bleiben sollen. Der eigentliche Druck / Druckbild, wird über ein Gummituch aufgebracht.
Digitaldruck
Der Digitaldruck oder Foliendruck ist vom Druckprinzip vergleichbar mit dem, was im konventionellen Papierdruck zur Anwendung kommt. Jedoch sind Folien als Druckträger nicht mit Papier zu vergleichen, zu sehr unterscheidet sich hier der Farbauftrag auf die Folien. Der Digitaldruck auf Folien ist bei größeren Auflagen und Stückzahlen das wirtschaftlichere Druckverfahren. Es entfallen vornehmlich Maschinenrüst- und Einrichtungszeiten. Bei Foliendrucken hat sich der Solventdruck durchgesetzt, mit dem die besten Ergebnisse auf Folien zu erzielen sind.
Hoch- bzw. Buchdruck | Anilin- und Flexodruck | Ind. Buchdruck – Offsetdruck | Tiefdruck | Heißübertragdruck | Siebdruck | Prägedruck | Farbspritzen | |
---|---|---|---|---|---|---|---|---|
Flächendruck einfarbig | + | + | + | + | + | + | + | + |
Flächendruck mit ausgesparten Einzelheiten | + | + | + | + | + | + | + | + |
Darstellung feiner Einzelheiten | + | + | + | + | + | + | + | – |
Rasterdruck | + | – | – | + | + | + | – | – |
Halbtonwiedergabe | – | – | – | + | + | – | – | – |
Naß-in-Naß-Druck | – | – | + | + | – | – | – | – |
Metalleffekte | – | – | + | + | + | + | + | + |
Leitfähige Drucke | – | – | – | – | – | + | – | – |
Knoterdruck | + | + | + | + | – | + | + | – |
Dicke des Farbauftrags | mittel | dünn | dünn | dünn | dünn | dünn | versch. | versch. |
Glanz des Druckbildes | + | + | + | + | + | + | + | + |
Deckkraft der Farben | + | + | + | + | + | + | + | + |
Höchste übliche Farbenzahl | 4 | 6 | 4 | 6 | 4 | 3 | 2 | 3 |
Trockenzeit der Farben langsam |
+ | + | + | |||||
mittel | + | + | ||||||
schnell | + | + | + | |||||
Kleinstmögliche Schriftgröße in Punkten | 3 | 3 | 2 | 2 | 5 | 8 | 12 |
Tabelle: Möglichkeiten und Eigenarten der Druckverfahren
Flexodruck | Tiefdruck | |
---|---|---|
geringe Klischeekosten niedrigere Investitionskosten relativ kleiner Platz und Energiebedarf 1 bis 2 Bedienungspersonen kurze Umstellzeit bei Maschinen mit motorbetriebener (und computergestützter) Farbwerks-schnell-Verstellung und Vorregistereinstellung geringe Ausschussquoten (ca. 2%) eigene Klischeeherstellung bei relativ geringem Investitionsaufwand möglich Druckergebnis vom Aufkleben der Klischees und vom Drucker abhängig begrenzte Standzeit der Klischees |
hohe Formzylinderkosten höhere Investitionskosten großer Platz und Energiebedarf 2 bis 3 Bedienungspersonen kurze Umstellzeit bei Versionen mit Farbwerkseinschübenetwas höhere Ausschussquote (ca. 3%) eigene Formzylinderherstellung nur bei großen Investitionen und mehreren Tiefdruckmaschinen wirtschaftlich Druckergebnis vom Drucker fast unbeeinflussbar hohe Standzeiten der Formzylinder für Großauflagen |
Tabelle: Tiefdruck und Flexodruck im Vergleich
Die Einsatzgebiete in der optischen Veredelung sind sehr breit gefächert und unsere Geschäftskunden aus Handel und Industrie stellen immer größere Ansprüche, insbesondere in der dekorativen Veredelung, an uns. Zu den gebräuchlichsten Verfahren zählen unter anderem das Kennzeichnen / Signieren, Lackieren, Prägen / Heißprägen und Etikettieren.
Beflocken:
Durch Beflocken werden aus glatten Folien, weiche Flächen, wie man sie beispielsweise auch bei Kunststoffverpackungen kennt, bei denen, meistens auf der Verpackungsinnenseite, eine Beflockung erwünscht ist. Beim Beflocken werden sehr kurze Fasern auf einen beklebten Trägerstoff aufgebracht. Dabei entsteht der gewünschte Stoff- oder Plüscheffekt. Sonst harte Kunststoffoberflächen, werden in diesem Verfahren mit einer weichen Schicht überzogen, die dadurch entsteht, dass Fasern gerade auf der Oberfläche fest werden.
Beflockungsanlagen arbeiten in der Regel elektrostatisch. Leitfähiger Kleber wird auf den Trägerstoff ausgebracht und elektrische Felder erzeugt, in denen sich der Flock senkrecht aufflockt. Voraussetzung dafür ist, das Fasern zum einen lang genug sind, um senkrecht auf dem Trägermaterial verankert zu werden, aber auch die Faser selber elektrisch aufladbar sein muss. Zu Verwendung kommen vielfach PA Flocken, da sie über die sehr gute Eigenschaften verfügen. Die elektrostatischen Felder weisen circa 100 kV Gleichspannung auf. In einem abschließenden Schritt wird das beflockte Material mit Heißluft oder in Kontaktgeräten ausgehärtet.
Aluminium wird in Reinform bei rund 1700 Grad Celsius in einem Hochvakuum verdampft, um sich auf der Folie niederzusetzen und eine metallische Oberflächenwirkung zu erzielen.
Funktionale Veredelung
Neben zahlreichen funktionalen Veredelungsverfahren, sind Beschichten, Laminieren und Metallisieren ein zunehmend wachsender Bereich in unserem Unternehmen geworden.
Beschichten:
Als Beschichten bezeichnet man das Auftragen einer Thermoplastschicht, die es technisch möglich macht, eine dickere Schicht, als durch Lackauftrag zu erreichen. Man unterscheidet in Tauchbeschichtungen, bei denen Verpackungen, Packmittel, Packstoffe in ein Schmelzbad gegeben werden, wodurch sich ein Schutzfilm auf das Material legt. Man geht aus Umweltgründen immer mehr vom Beschichten mit Lösungsmitteln, zu einem Beschichten ohne diese Stoffe über.
Laminieren:
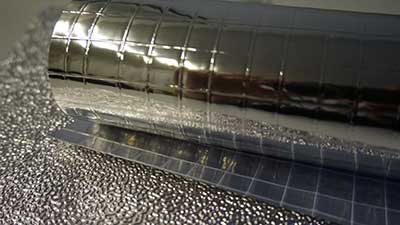
Oberflächenveredelung von Kunststoffverpackungen
Als Laminieren oder Kaschieren bezeichnet man das Verbinden von zwei Materialbahnen, die vielfach als Rollenmaterial verarbeitet werden. Bestehend aus zwei Einzelschichten erhält man so Verbund-oder Doppelfolien. Heute ist das Coextrusionsverfahren das verbreitetste Verfahren. Man unterscheidet hier in Nasskaschieren, wenn Haftvermittler oder Klebstoffe beigefügt werden. Beim Trockenkaschieren werden zwei flache Packstoffe mittels Klebstoffen (lösungsmittelfrei und auf Wasserbasis) verbunden.
Beim Heißkaschieren / Thermokaschieren werden i.d.R. Folienbahnen nur unter Druck miteinander verbunden. Hierbei kommen keine Kleber oder andere Verbindungsstoffe zum Einsatz. Man bezeichnet sie als Kaschierfolien. In diesem Verfahren lassen sich hochwertige Folien herstellen, die auch als Packstoffe aus Papier oder Pappe Verwendung finden.
Beim Flammkaschieren findet eine Werkstoffverbindung über Erhitzung durch Beflammung statt. Vielfach werden aber auch Infrarotheizungen zum Aufheizen der Oberflächen verwendet.
Metallisieren:
Als Metallisieren bezeichnet man ein Verfahren, bei dem Oberflächen so veredelt werden, dass eine metallische Oberflächenwirkung erzielt wird. Hierbei wird der Trägerstoff in einem Vakuum mit einer metallischen Schicht überzogen, die über die Gasphase auf das Trägermaterial übergeht. Die Metallisierung erfolgt so, dass in einem Hochvakuum ein Kunststoff eingebracht wird, der Kleber enthält. Durch Erhitzung verdampft das Belagmetall und legt sich auf die Kunststoffoberfläche.
Metallisieren von PP-, PA- und PE und Polyester-Folien mit Aluminium
Das am häufigsten eingesetzte Belagmetall ist Aluminium. Es findet eine Metallisierung durch Aluminiumbedampfen bei diesen Folientypen statt. Bei Verbundfolien entsteht die Metallisierung in der Innenschicht. Aluminium wird in Reinform (AL 99,98 R) bei rund 1700 Grad C in einem Hochvakuum verdampft. Hierbei setzen sich die Metallatome auf der Folie nieder und setzen sich an der Oberfläche fest.
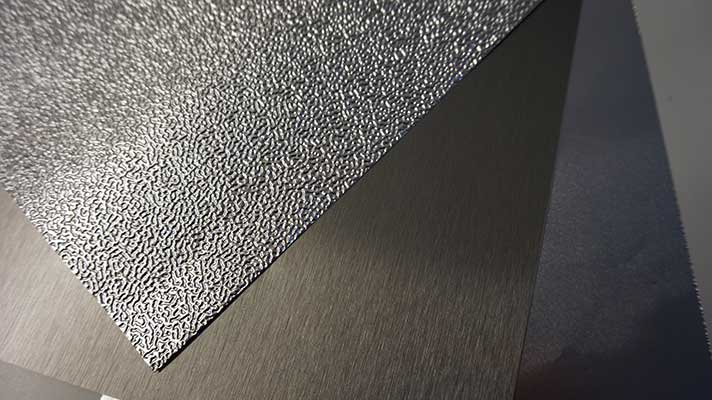
Oberflächenveredelung von Kunststoffverpackungen
Erfahren Sie mehr überd die Oberflächenveredelung von Kunststoffverpackungen – kontaktieren Sie uns!